Enamel dial: sophisticated hand work
Enamel – a vitreous transparent alloy, consisting of quartz, soda, chalk, magnesium carbonate and litharge. This strange mixture of different ingredients is easily processed. It is similar to porcelain and glass by its structure. Enamel looks as colorful and luxurious as jewels. Enamel is obtained through burning silicon crystals, mixture of magnesium and borax. The material is processed by heating: at high temperatures enamel is melted the same way as glass.
The history of some alloy
The word enamel comes from the High German word “smelzan” later becoming “esmail” in Old French. During centuries enameling was called by different craftsmen in different ways: however, all those words could only slightly convey its amazing features and beauty.
Enameling passed a long path of development, started in far ancient civilizations: Egypt, China, India and Byzantium became its place of birth. Then it came to medieval Europe.
Today enamel is successfully applied in various fields: architecture, interior design, jewelry and watchmaking. Enamel took a special place just in the watchmaking, particularly in making original and unique dials. We will tell you about this below.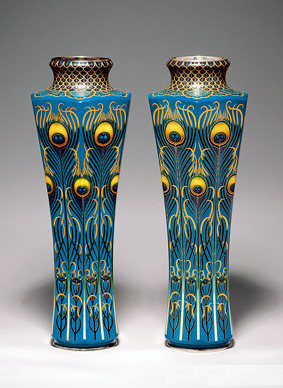
Enamel dial is a completely special trend in the modern watch industry, as a small miniature hides a long way of development and experience, various techniques and secrets of craftsmanship. But at first a few words about history…
***
Enameling roots back in far past. Brightness and rich colors, shine and luxury, equal to beauty of jewels, and great art abilities – this is an incomplete list of enamel’s features that have been attracting graphic artists, sculptors, including of monuments, artists, jewelers and watchmakers since many centuries.
The process of metal and glass fusion, incrustation of metal with multicolored insets – all that was known to the masters of ancient Egypt, China and India. That’s why the ancient ware and adornments of these countries strike imagination by their perfect quality of performance, elegance and delicacy of work even today.
Ornamental art of ancient world became the first model inspiring many modern masters. Gradually enameling spread in ancient Greece and Rome in the first centuries AD. High demand, popularity and wide use of enamel inspired craftsmen for constantly looking for new forms of its application. Enamel was an adornment of women attire: pendants, necklaces, diadems, and earrings were made with the use of enamel; also the material was applied in finishing of crockery and church plate, different household things. Enamel was also used for adornment of things for men. So, the trappings and weapons were adorned with it. Usually enamel was combined with stamping, precious stones and engraving on silver and golden base.
Byzantium enamel – enameling classics
To see the complete picture of enamel appearance and development we should study the origins of European art. At its careful consideration one can safely say that enameling came from Asian countries, especially Eastern. Those countries indeed contributed their specific style in enameling and development of various technologies, which were used in the Mediterranean area up to present days.
However, just Byzantine enamel, its appearance and development are considered by the history as a classic image of enamel, although the Celtic-Roman champlevé enamel appeared 500 years earlier, and some Egyptian incrustations by cloisonné enameling are millennium-older than Byzantine enamel.
When enamel spread from Egypt, China and India to ancient Greece and Rome, it became one of the most popular materials, like precious metals. So, the processing of precious metals became especially popular in late ancient Byzantium. In time the processing of precious stones also became popular, and later the first prerequisite for combining metal with glass appeared.
An incredible luxury reigned in Byzantium in that period. In many cities, especially in the capital – Constantinople (present Istanbul), the churches and palaces were faced with golden mosaic. Interior thing, marks of high classes’ distinction, sacred vessels – all that was an example of luxury and fine work. It can be supposed that Byzantine enamel was developing mostly as a fine art: champlevé and cloisonné enameling were seen in the design of solemnly strict icons, so remote from earth reality. There are records, referring to the period of reign of Justinian (VI century), which prove a significant high level of these techniques development in that period. Unfortunately, many of those beautiful things were destroyed during “aniconism” in the period of 726-843.
The golden age of enamel in Byzantium was in the XII century, after which a collapse happened. However, the short-term experience of Byzantium in exploration of enameling techniques turned out to be decisive in its development at the periphery of the Byzantium world: Serbia, Kievan Rus, Georgian, and Armenia.
The famous dish of emir Davud covered with cloisonné enameling from both sides can be separately noted as an example of Eastern technique. According to the inscription, it belonged to emir Davud (1119-1144), who had a residence in the Upper Tigris. The Ascension of Alexander the Great is depicted in the middle of dish. The unique dish remained only thanks to a chance, and today it is a wonderful example of the Byzantine enameling. According to the researchers, the design of that dish combines elements of the Byzantine, the Persian styles and style of a bit later antiquity.
The ancient enameling was highly valued that could be caused by complicated technical process of making enamel mass. So, the art of enameling was brought to perfection in Byzantium, concerning both purity of colors and variety of art designs and unusual shine, brightness, durability and hardness, thanks to which enamel became so popular and specific. Complicated composition and exclusive art values became a specific feature of enamel, told us by Byzantium chroniclers. There is a record about the construction of the Cathedral of St. Sophia in Constantinople in the second half of VI century by emperor Justinian, who ordered enameling of his altar golden throne.
Very few enamel items, aged up to the X century, remained; therefore, it’s quite difficult to the researchers of enameling to tell something about techniques of that time.
The golden age of Byzantium enamel was in the X-XI centuries: the pieces of cloisonné enameling became mostly popular by both art values and technique of performance. The XII century became a start of enameling decay, and the pieces of the following century acquired a cruder and stereotyped character. Gradually the technical qualities of enamel and past durability of the material faded away, the color combinations became harsh, and the best colors of enamel were lost…
Color tones of enamel
Different tones of enamel are obtained by means of various metal oxides. For example, manganese oxide gives brown and violet tones; iron oxide in combination with other components dyes enamel in yellow, red, grey or black colors; brass oxide gives blue-green color. Enamel can be transparent or non-transparent (or opaque enamel, as masters name it). Lead oxides make enamel transparent and pure; non-transparency is a result of adding opacifiers, like tin, kaolin, bone flour.
***
Today enamel is as popular material for finishing and decorating various things, as it was many years ago. Enameling went through several stages of development: use in ancient civilizations, great popularity in the Middle Ages, complete oblivion and renaissance in the XIX century.
Today enamel has taken its special place in jewelry art, interior design, ornamental art, and even in architecture, as it is one of the most solid materials, keeping color and structure, regardless weather changes. The features of enamel are bright paints, shining smooth surface, deep and intensive colors, and clear contour pattern. All these qualities require compositional decisions.
Nowadays, as well as in ancient times, floral ornament is one of the most popular elements. However, the modern watchmakers, who changed enameling into a full part of horlogerie, went further than simple ornaments. Sometimes the masterpieces of the world and portrait art are reproduced on small enamel dials, the wonderful symphonies of beautiful pictures are performed. The enamel things are specifically small. That’s why this kind of art is so popular in the watchmaking.
While the traditions of Eastern decorative art gave a role of design material to enamel, like incrustation or stamping, the unique alloy became a complete art field in Europe, resulted by the appearance of the first pocket watches.
Pocket watch – a picture round the neck
Initially the pocket watches were sooner “neck” watches, as nobody held them in his pocket. They became real pocket things only in two centuries. The term “pendant watches” perfectly revealed the way they were worn in those times.
The pendant watches trace their roots in 1510. Then they had a ball form, and only by 1630 they acquired a usual form: round case with cover.
The first watches raised doubts in their movements’ accuracy, therefore, they were taken, first of all, as an adornment. That’s the reason why their design took so much time – not less than the decoration marks did. For the design of cases the watchmakers applied such techniques, as Cloisonne and Champleve, which remained popular up to present day among modern watchmakers of lux companies. Speaking about complexity, both patterns are complicated and require accurate meticulous work, especially when the working area is a small watch case, its cover or dial.
Champleve is a technique of enameling, by which miniature cells are cut in golden base and filled with various tones of hot enamel layer by layer.
Cloisonne is much more difficult that Champleve, as it is based on a “net” of golden thread, which sometimes reaches 100 meters in length and about 0,3 mm in diameter. The thinnest net fixed on metallic surface is filled with separate multicolored fragments of enamel, composing a pattern. The golden thread itself becomes invisible after that. That’s why Cloisonne patterns looks more detailed and natural that Champleve.
However, neither Champleve nor Cloisonne can compete or compare with real art, as they don’t reproduce the depth of picture, play of lights and shades, tones…
Dial enamel miniature
Enameling would have stayed in the category of ornamental jewelry techniques, if a real revolution in enamel miniature hadn’t happened in the XVII century: a small room of dial became a canvas for the boldest ideas of artists. Enamel miniature and watches appeared practically at the same time. There that “relationship” came: very soon enamel miniatures became the “second face” of chronometer.
Enamel dial miniature was born in the French city of Limoges. The history started by two Limoges masters Penicauds and Reymonds, who designed their own technique of applying oxides on metal surface, and soon the Limoges miniatures were applied for adornment of the most Paris pocket watches of the XVI century. They could compete even with the Limoges porcelain in their popularity.
However, Eure-et-Loir and Loir-et-Cher with its capital Blois received the title of miniature art center. According to historic facts, miniature art became popular mainly thanks to the war between Catholics and Huguenots.
The Edict of Pacification, proclaimed by Henry IV in 1598, influenced on situation of artists: hundreds of Parisian watchmakers and artists moved from Paris to protestant city Blois, which thanks to such migration turned into a leading cultural center.
26-year old jeweler Jean Toutin was among the migrating artists. That was him who invented the enameling technique, which wasn’t inferior to oil painting in either quality or depth of picture. A pointillistic manner of enameling became the base of technique. Pointillisme is a French word, literally meaning “dots applying”. Pointillisme became a new trend of neoimpressionism art, appeared in France in about 1885. It a method of painting with dots to achieve various affects. The dots can be placed singly, in rows, or randomly.
Jean Toutin’s method consists in graded burning: the artist-miniaturist creates a miniature landscape or portrait on burnt white surface with the help of thin brush (or even hair) by the method of artists-pointillists. Light tones were burnt in furnaces, and then the artist continued painting by darker tones. As a result of consistent painting and burning the artist achieved the highest accuracy of picture and most delicate color nuances. At the end of work, after burning and polishing, a transparent enamel layer – fondant – was applied, giving agleam depth to the picture. That method gained such success that soon Toutin had many apprentices, who later formed the school of Blois. Such famous miniaturists, as Pierre Chartier, Duby, Christophe Moliere, and Isaac Gribelin, more famous as a stamper, were among the apprentices of the great master.
In 1622 Toutin returned to Paris, where he designed pocket watches by English, German, and, of course, French craftsmen. Little by little Toutin’s works became popular, and the miniatures on covers and dials passed through the English Channel.
So, in 1635 Simon Hackett made a golden watch with a picture of landscape on the cover in the style of Toutin’s school. The watch attracted much attention, and the newspaper “Journal des Savants” wrote in September 14, 1676, that jeweler Toutin from Chatodan achieved perfect craftsmanship in enameling of historical scenes and portraits that could be compared only with oil painting. However, the school of Blois was recognized later. As a result of Huguenots’ expulsion to France, the center of jewelry and horlogerie moved to Geneva, and the end of XVII century became “the first death” of enamel miniature.
The death was caused by a range of inventions: in 1675 Christian Huygens invented a pendulum regulator, the watches with balance springs became more accurate and consequently more utilitarian things, which didn’t require a special design. The minute hand and the glass, covering dial, appeared, and soon the watchmakers started doing their best to constantly improve movements. The watches moved to pockets, and a bright design became excessive. Soon enamel pictures were completely replaced by guilloche.
As the mass production and the so-called New art appeared, enameling “died” one and for all. That process could be called quite natural, considering that creation of only one picture took 250 hours and such things were issued in single copies. Besides, enamel turned out to be of little use for the new trend of abstract and impressionistic art. Neither bright colors, good for flowers, portraits and landscapes, nor non-fading paints saved enamel…
Enamel in watchmaking: renaissance
A question may arise: what is horlogerie after all? Many people will say this is watch movement, its complexity, skilful and beautiful engraving. Others will answer that a worthy design of movement – case, incrustation, dial – is not only a “beautiful” addition to the movement, but also a separate and complete sphere of watchmaking, which plays a quite significant role in creation and choice of chronometer.
No matter how different the opinions are, there is only one conclusion: interior and exterior components of chronometer harmoniously complete each other and can’t create the striking impression separately, as they do in “chronometer alliance”.
In the beginning of watchmaking, when the pocket watches were the only chronometers, which were not distinguished by high accuracy, their covers were decorated with enamel pictures. That was the time when a mechanical union of chronometer and enamel “decoration” was born.
At the time, when the watches were rather adornments than accurate time meters, enamel design was the main advantage of watches. But the technical progress, development of watch movement and appearance of minute hand displaced enamel pictures from cases and dials. But finally the watchmakers and their customers realized that complicated and accurate movements might have worthy design. That was the main condition for wrist watches to deserve no end of praise…
***
Mending of trade fences between Europe and China in the XVII- XVIII centuries greatly promoted enamel miniature renaissance. The Chinese emperor was crazy about “European things” and especially painted clocks. So, the Chinese emperor collection, before it was plundered during Kuomintang wars, included thousands of snuff-boxes and caskets with enamel miniatures, and also clocks.
In the XVII – XIX centuries Geneva became the center of enamel art. A few craftsmen and artists left in France were obliged to move to neutral Switzerland. At first, because of revolution, then because of Napoleon wars.
The history of enamel art counts about 80 artists and miniaturists, who worked in Geneva in that period, such as Jean Petitot, Pierre Bordier, Théodore Turquet, Liotard, Alexandre de la Chana, Jacques Thouron, Jean-François Soiron, Jean-Abrahant Lissignol, Henri L'Evêque.
However, Jean-Louis Richter is considered to be one of the most renowned masters of the XIX century, who created an enormous quantity of miniatures for the Swiss watch companies. His watches with erotic pictures, delivered at the Eastern market by many famous watch houses (Blancpain and others), should be noted separately.
Peter Carl Faberge, who actively used enamel in his miniatures, gave another impetus to the development of enameling.
Types and development of enameling techniques
During many centuries the art of enameling was constantly developing and improving. Based upon study of many antique enameling techniques, today some principal ones actively applied should be pointed out: champlevé, cloisonné, plique-a-jour, and grisaille. Such techniques, as Cloisonne, Champleve, or Grand Feu, were founded by the craftsmen from India, ancient Egypt and China. Usually they used a mixture of magnesium and cobalt. At freezing the mixture heated up to 12000 degree temperature changed into a uniform material of deep glimmering blue color. The craftsmen kept on working with it, coloring and making pictures out of it. And the Byzantine masters, for example, could obtain bright-blue enamel (called “Turquoise” today) instead of dark-blue by means of Grand Feu. The Byzantine technique of Grand Feu practically displaced turquoise insets in the Near-Eastern world…
Champleve – one of the simplest techniques of enameling, recommended for the beginners. That technique was mainly applied in the articles of ancient Greek and Roman masters of the first centuries AD. The Roman masters inlaid vitreous mass into special depressions in the metal, and next to gold, brass or silver, enamel created a beautiful play of colors and an illusion of precious stones or specific mosaics. The main principle of champlevé is specific depressions on decorated plain - “raised plain”. They are made by etching, stamping or fretwork. Enamel is inlaid into the depressions, and the pattern is ready.
Today champlevé is widely used in the mass production. So, thanks to applying high-technological punches, many manufacturers make bases for marks, emblems and other inexpensive adornments for women. Creating such items requires repeated infill of depressions by enamel, burning and, finally, grinding and polishing of the surface.
Cloisonne – a technique in which metal wires are bent to form a design; enamel is then inlaid into the resulting “cloisons.” Although this can be done in copper, contemporary cloisonné is most frequently done in silver or gold. French for “cloison” or “cell.” This technique is specific by hand work. Unlike champlevé, cloisonné doesn’t take mechanized making of a base.
Guilloche – French for “engine-turning.” Engine-turning is the mechanical cutting of lines on metal to create a design. This is one of the most laborious techniques, requiring great practical skills. The engraving causes the reflection of light through the overcoating of transparent enamel to be enhanced. This causes a brilliance which can be seen as the piece is moved from side to side. This technique of enameling was brought to prominence by Fabergé, Russian artist, when showing pieces in Paris in 1900.
Grisaille – this technique requires not only craftsmanship and meticulousness, but also abilities for painting. The procedure is as follows: first the metal base is covered with counter-enamel (enamel layer from the underside). Usually these are thin copper plates. After firing the surface is covered with enamel, which will be the background for picture, and burnt again. Then by means of special enamel paints a picture or a subject may be created. The firing of painted layer is a finishing stage of this uneasy and quite long process. After the painted layer is covered with another layer of protective transparent enamel and burnt again for the last time.
Plique-a-jour – this technique uses no metal base, but thin gold or silver wires. Or cells from a metal plaque are sawed out or etched, making small bottomless cloisons on the metal, which are filled with enamel and fired. You can see the picture through, as enamel used is transparent. The word “plique-a-jour” means “braid, or window, that lets in daylight”.
Stenciling – this technique is especially characteristic for making trays, plates, panel pictures, and others. Stenciling has become very popular recently. This is a technique in which a design is cut into a material, such as paper, through which the enamel is applied to the metal. For each color isn’t mixed with another, each layer is glued by means of sprayer. The firing is the same as in other techniques.
Grand Feu or Turquoise – a centuries-old technique of enameling, which came from ancient Egypt, China and India. Such items were distinguished by perfect performance quality, delicate work, multi-colors and elegance. Jewelries, crockery and various articles strike by their beauty and colorful performance.
This technique consists in applying the meticulously prepared enamel powder onto the dial’s base plate and fusing the two together by heating them at 840 degrees temperature. The intense heat is due to the high melting point of the enamels and this is why this type of enameling is referred to as grand feu. The perilous firing operations at extremely high temperatures make it possible to show incredibly precise details.
There is no consensus among scientists on the place of grand feu birth. Some researches affirm that the technique over 1000 years ago in China, others suppose grand feu came from Byzantium of the IV century. Also there is a point of view about Eastern countries, where grand feu was born in the X-XI centuries AD. And the scientists have reached common ground only in one issue: grand feu is one of the best ancient and prestigious techniques of enameling.
There are records that Chinese emperors were keeping track of that art in the XII-XIII centuries, contributing in the development of bronze casting and hot enamel combination. So, blue enamel appeared, being a visiting card of China in that period. Grand feu was used for decorating various household things, chopsticks, interior items, various adornments. The technique was developing little-by-little, and the craftsmen learned to apply hot enamel on both bronze and copper. Different colors of enamel were obtained.
Grand Feu today
The model technique of grand feu includes several stages. The first one creates an item from pure copper. Pure copper is lack of mixtures, which negatively affect the item’s quality, therefore, the craftsmen prefer it. Then special hollows are pressed in on the base, which are filled by special mixture, containing water and painted powder. The dried dial undergoes a first firing at a temperature of around 900-1000°C in order to be able to withstand the many subsequent firings in the furnace. After around twenty firings in the oven the colors are vitrified by the heat and progressively change, become more intense and retract.
At the final stage the item is generally coated with two or three layers of a finishing flux consisting of transparent enamel serving to protect the work from the potential effects of ageing. When the final firing of this flux is done, a fine polish with an abrasive stone is performed, followed by the final polishing operation after the last vitrification in order to achieve the full radiance and pictorial splendor of the work.
Grand Feu in horlogerie
In horlogerie “hot enamel” is called “grand feu”. This technique is the same as cloisonné: enamel powder applying with the following firing.
The Geneva technique of miniature enameling with a protective flux coating is undoubtedly that which requires the greatest expertise from the master enameller. Some watch companies reproduce masterpieces of the world art and portraits on their dials! On a white enamel base serving as a “background canvas”, the artist starts by making outlines of various motifs with a brush consisting of two or three marten’s hairs. This involved a few touches of color on the chosen shade, placed in an precise order from the softer shades to the purer, brighter ones. The extremely fine powders and pigments used for miniature enamel paintings are blended with oils such as lily flower oil, to make them easier to apply.
Grand feu, making watches luxurious and unique, can be afforded by few watch companies. As this technique requires high craftsmanship and delicate taste, combined with skillfulness.
Enameling is a well-lost art
If you look through some specialized edition, you may think that the enamel techniques are buried in oblivion today. However, this is not true. In fact, the proportions and techniques are known to everybody – they are published in various magazines, internet. The craftsmanship is what has been lost and most difficult to recover.
Today many watch companies have set a quite difficult task: to recover lost enamel art that some companies have succeed in. These companies turned enamel art into their distinguishing feature (for example, Bovet).
Today enamel art becomes popular in the watch industry again, proved by the exhibitions in Geneva and Basel: enamel picture becomes a trend.
Besides all advantages of this material, an enamel dial is also specific for its exclusivity. The miniature picture or the portrait on your dial, made from enamel, is a laborious work, unique and worthy of admiration…
Modern “enamel” companies
So, today enamel art is a prerogative of enthusiasts, based on personal experience, worming secrets of craftsmanship out of remained artists.
It should be noted that today there are no specialized school or enamel art course in the ex-center of enamel art, Geneva. Of course, a question may arise: where do the craftsmen, creating beautiful miniatures for dials, come from?
In fact, there are very few artists, painting dials, today. Some companies, famous for its enamel dials, do not recruit masters all the time. Some brands have their own secrets of manufacture, which let them save both money and time. So, the templates are prepared: one element (for example, a bird or a flower) isn’t applied on white enamel by brush or by hand, but by stamping. Although, a real enameller will never go down to this.
Enameling is a difficult process, requiring dozens of hours: enamel might leak and spoil the meticulous work any second. However, only such work can result in “eternal” and priceless pictures. Today enamel art takes a special place in the watch industry. Many big companies have got involved in studying the techniques of medieval masters, and today they present original items, which lay claim to the title of “masterpiece”. So, the watch companies “Patek Philippe”, “Jaeger-LeCoutre”, “Bovet”, “Cartier” present plenty of enamel miniatures that can compete with antique items in their beauty and craftsmanship…
P.S.
Speaking about big clocks, their movements are closely connected with sculptor, art, and architecture. But we’ve been telling you about wrist watches that inherited beauty and “watch grace” from pocket watches, and architecture forms – from big “large-caliber” wall clocks.
The jewelers, engravers, artists-miniaturists didn’t contribute in decoration of wrist watches and exaltation of horlogerie less than the engineers-watchmakers themselves. So, nobody can say who was a greater watchmaker in the XVIII century: an unknown craftsman, working in the Royal workshops of Versailles and assembling faceless movements, or a court jeweler, who shaped a movement into an amazing and unique case.
One should always keep in mind that initially mechanics and design appeared as a single unit – movements without decorations didn’t strike imagination of connoisseurs, and while mechanical achievements were known, first of all, to the collectors, appearance of chronometers is seen and valued by everyone, who has bought a Swiss wrist watch at least once. Watch is still associated, first of all, with dial, but not movement. And, of course, the material this dial is made of is very important.
Enamel can be called an integral part of Haute Horlogerie. Today more and more watch companies issue wrist watches with enamel dials, revive the traditional art of enamel miniatures, adorning dials and cases of wrist watches.
Today in the best watch salons of the world along with usual terms “Reserve de Marche” or “Tourbillon” you can hear the intriguing names “Champleve”, “Cloisonne”, “Grand Feu”. The traditional and almost medieval values return to the modern watch industry. As hand work is valued much higher, great attention is paid to various techniques, performed only by hand.
Enamel art is alike watch movement: it also requires hard meticulous work, precise motions and craftsmanship to obtain a masterpiece, striking imagination. Enamel miniature represents the most valuable piece of art and flight of thoughts, which is out of time and technical progress. Thanks to enamel art the craftsmen literally return to the past: the professional enamellers use the same art techniques and instruments, used by their predecessors 300 years ago.
And, finally, if the originality of a watch movement might cause doubts sometimes, an enamel miniature is original for 100 percent. Buying an enamel watch, you become an owner of a true value that will remain for years. Longevity is one of the main features of enamel: it doesn’t age, it’s not affected by humidity or light, it doesn’t change its colors. Enamel art is like a watch front, admired from the first glance.
Tourbillon Relatif New York from Piaget
The wrist watches of Piaget are interesting for people with completely different tastes. The company manufactures jewelry accessories and wrist watches, harmoniously combining technical component with elegant design.
Piaget traces its roots in 1874. The founder of the company – Georges-Edouard Piaget, who established his highly-accurate watch movement-manufacturing workshop in picturesque city Côte-aux-Fées. In the beginning the workshop simply provided the famous watch companies with movements. In time the production expanded, and the watches from Piaget became a symbol of exclusive craftsmanship, and the manufactory began its business in the world “watch capita” – Geneva.
The manual-winding caliber 9P of about 2 mm thickness, created in 1957, was the first ultrathin watch movement of Piaget. In 2010, the company issued a watch collection with titanium cases. After that, at the exhibition SIHH, another thinnest model in the world with automatic movement “Altiplano Ultra-Thin” appeared. Today the company makes movements of new generation 1200Ð and 1208Ð, which are only 2.35-mm thick, being the thinnest automatic calibers in the world.
Mainly the companies, releasing wrist watches, divide their collections into two types: the watches for everyday use and the watches that could be interesting for collectors. But the creative stuff of Piaget designing new models considers the conditions, in which the watches will be worn. That’s why last years the craftsmen put a special accent on three main trends: ultrathin watches “Altiplano”, jewelry collections “Miss Protocole” (a collection of women wrist watches with interchangeable straps and bracelets) and sport watches (collection “Polo Forty Five”).
Among various products presented by Piaget one model can be marked out – the watch, devoted to New York. The model “Tourbillon Relatif” is inspired by the city, which became a shelter and muse for many talented and famous people. The company’s representatives note that now the fans of the megapolis can wear not only the T-shirt with “I Love NY”, but also wrist watches, devoted to the Big Apple. Although the chronometer can’t be compared with a T-shirt for sure, and only a few people can afford this accessory: Tourbillon Relatif is released in a limited edition of only three pieces.
This model is inspired by the architecture of the famous city. The watch “Tourbillon Relatif” is also an embodiment of enamel miniature, presenting the most significant and famous buildings of this city. The model is equipped with in-house hand-wound movement “Piaget 608P”. The case is made of 18-carat white gold. The case is engraved with the panoramic sight of Manhattan with its two main bridges on one side, and with the panorama of the city and the Statue of Liberty on another side. The flying tourbillon with titanium carriage, situated on the minute hand, became the main technical feature of the caliber. However, neither precious metal the case is made of, nor its original engraving, nor even in-house movement became the main design decision. Its true adornment is a black dial, made of enamel by Grand Feu technique. Twelve highest and most famous building of New York are situated between Roman numerals. The black strap is made of natural alligator leather. Simplicity and elegance made this model successful. But don’t forget about only three lucky bargees, who will get these watches.
Bovet – enamel art
The products of Bovet can be characterized as a sophisticated feast for the connoisseurs of original accessories. Each model by Bovet is a piece of art in miniature. The best engravers, miniaturists and enamellers work on each item.
The company is founded in 1822. However, the history of Bovet started from the moment when its founder Eduard Bovet together with his brothers Frederick and Alfonso moved to London, considered to be the European center of watchmaking and trade at that time, to improve his skills in horlogerie.
In 2011, Pascal Raffi, who respected the heritage of Bovet and revived taste for traditions and enamel miniatures, became the main share-holder of the company. According to Pascal, the initiative of reviving the connection with past became a special story. At one of his first meeting with the main distributors Pascal had to answer the question about exclusivity of Bovet. Then Pascal asked the distributor to put watches of two different brands on the table, turn off the light and add his own wrist watch. When they turned on the light, the merchant could identify only his chronometer, unlike two other brands. However, when the watch from Bovet took part in that experiment, the future distributor knew it at once.
The point is in its crown construction and original design of case. From 1998 to 2000 Bovet manufacture watches with crowns at “3” hours. However, the return to past epoch styles motivated the designers to look for a design in “pocket watch” style – so the crown moved to “12” hours. The story with the distributor made Raffi keep the antique and already traditional design of crown.
Many watch models from Bovet received various international awards thanks to original design of case: the watches by Bovet became a standard of craftsmanship in making high-accurate movements. However, there is one more feature of the company that makes its watches unique and recognizable, attracting much attention: miniature art of dial, combining various techniques of enameling.
The masters of the company create a miniature picture on burnt white surface (mainly golden or cooper plate) with the help of thin brush (or even hair) by the method of artists-pointillists. Light tones are burnt in furnaces, and then the artist continues painting by darker tones. As a result of consistent painting and burning the artist achieves the highest accuracy of picture and most delicate color nuances. At the end of work, after burning and polishing, a transparent enamel layer – fondant – is applied, giving agleam depth to the picture. The creation of dial by this technique might take up to three months of laborious work, as only one wrong motion can spoil everything.
The collection “Miniature Painting” from Bovet is an excellent example of enamel art, embodied at the small space of dial. The masters of Bovet work by a special technique, combining old traditions of enamel art with modern methods, resulted from their own designs. Each model from this collection is a colorful image, telling a unique story.
|